Thanks to work already completed, most of the panels on the shell were in good condition however there were a few items I had to fix from when I had a 3rd party complete the rust repairs. When the replacement sills were fitted, the guy managed to misalign the side body panel with the sills. I had to split the side panels and sills, do some panel beating then weld them back together.
Drivers side before (outward bulge at the rear of the door opening) :
After repair :

Passengers side behind the door opening (significant 7mm indent) :
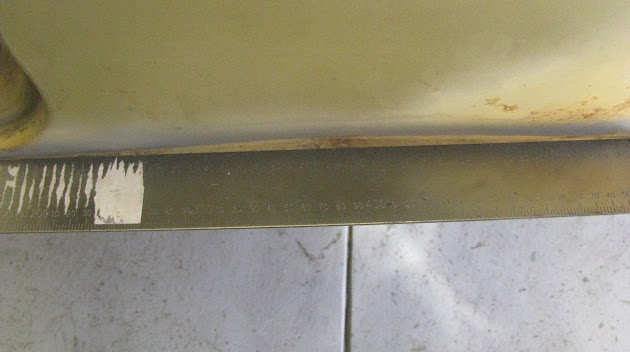
After the repair, there was still a very slight indent (just over 1mm) but much better than what it was.

The roof gutters were also fixed as they had multiple dents around the roof :
These were fixed with some gentle work with a crowbar, and steel plate to support the roof panel :

While working on the roof gutters I scraped out all the old hardened seam sealer with a pick.
The other area to work on was various dents around the shell. I spent a few hours with hammer and dollies, mainly on the floorpan and boot floor which were both badly dented in multiple areas.
A significant amount of time was spent on general clean up of welds all over the shell, including a final pass over the shell with a torch at night to mark any pinholes to repair, of which there were quite a few. The result of a couple of days of welding/grinding was a thick layer of grinding dust on the workshop floor :
The door panel gaps also had to be adjusted. With only myself working on the Mini, I found it hard to hold the doors in place while adjusting them so I made a couple of 3D printed tools for this job, which will also help during final assembly. Firstly a custom two-piece tool to hold up the top of the doors from the roof gutter and allow fine adjustment with the clamps.
I also made and printed some panel gap gauges with inset magnets for aiding in the minor adjustments.
To also make it easier to work on the doors when off the body, I made a panel stand using some old tent poles among my steel scrap and covered the top rails with pipe insulation foam. Using extendable tent poles also allows me to adjust the height between 900mm and 1100mm.

Most of the door gaps were good with even 4.5-5mm gaps however the lower corners were very tight.

The correct radius for both doors was marked, cut back and welded/shaped.
The body seams needed some attention to straighten areas such as window and door openings where the factory spot welds have caused some substantial wavy areas.
Before :
After :
The driver door had some minor dents to fix, as well as damage to the lock where probably an attempted break has damaged the lock opening.

The shell was treated to a degrease and pressure wash, then an air gun used to blow out water from various crevasses. The doors, bonnet and boot-lid were also cleaned and I confirmed the water drain holes in the doors were working well.

Comments
Post a Comment